Customers - Customer Interface Module
Customer interface module - the AIMS/ERP Customer
Interface Module (CIM) is a large-scale, sophisticated subsystem
within the AIMS/ERP system. Key functions are summarized below,
including several diagrams that describe its primary data stucture and
subsystems within the overall module.
Multiple distribution channels - AIMS/ERP is built from the
foundation up to support a complex multiple channel sales process.
each customer has one or more type codes assigned to it, which in turn
provide linked access to screens containing type-specific data.
Each customer type code is linked to and controls the specific
products and pricing structure that can be sold through that channel.
These function as mutually exclusive product catalogs, in effect,
separate for each distribution channel.
Thus a licensed dealer can buy product licensed for sale through that
channel, at its specific price structure.
Another customer type can, for example, be sold only spare parts for
that channel, while another customer type can be offered only
promotional products such as coffee cups and t-shirts.
Project / Job Management - AIMS/ERP includes the
ability to define a project / job of any complexity by linking Work
Orders together to form a Work Breakdown Structure (WBS), accumulate
estimated work/cost data, vendor quotations for custom parts or
subcontracted work and other project-specific functions. This
major functionality includes:
-
Job/Project Quotation - creates
a set of linked Work Orders that have a status that excludes them
from production & material scheduling, all of which are linked to a
Quotation in the Sales Orders table. The Quotation is turned
into a Sales Order via a simple function, which in turn changes the
status of the Work Orders, placing them in production.
-
Estimate to Completion (ETC)- cost rollup of
all budgeted (remaining) work to provide a "work remaining" cost.
-
Actual Cost Incurred to Date (ACI) - rolled up
costs for all actual work performed, including purchased material,
subcontracted / vendor performed work, and internal labor cost.
-
Estimate at Completion (EAC) - rolled up total
of the budgeted/remaining cost in the project plus the Actual Cost
Incurred to Date to calculate a projected total cost that will be
incurred by the project's completion.
-
Project baseline WBS - this provides captures
all of the project's WBS detail as it was at the beginning of the
project/job, as the "live" WBS structure can/will be changed during
the course of the project. It was designed to enable a
detailed comparison of the baseline with the current state of the
project at any point. Development of this function was in
progress when we closed the company, and so it is incomplete.
-
Mixed Mode Operations - the AIM/ERP Project/Job
Management function can be used concurrently with any other
production/management modality, such as work order production or
repetitive production.
-
Mixed Mode Costing - AIMS/ERP provides a
concurrent standard cost functioning with accumulation of actual
costs incurred for purchased material, purchased services, labor
cost. So a project can be estimated using a mixture of
standard and one-off quotations, the tracked during its completion
with variance reports either comparing incurred costs to standards,
or to estimated unit-level costs. We had previously designed,
built and implemented a full actual product cost system for a
division of Hughes Aircraft earlier in our career. The
AIMS/ERP costing functions utilized some of these lessons learned,
but without the very complex data & processed required for full,
detailed, and on-going actual cost of produced items.
The diagram below provides an overview of the integrated AIMS/ERP
Job/Project Management functionality.
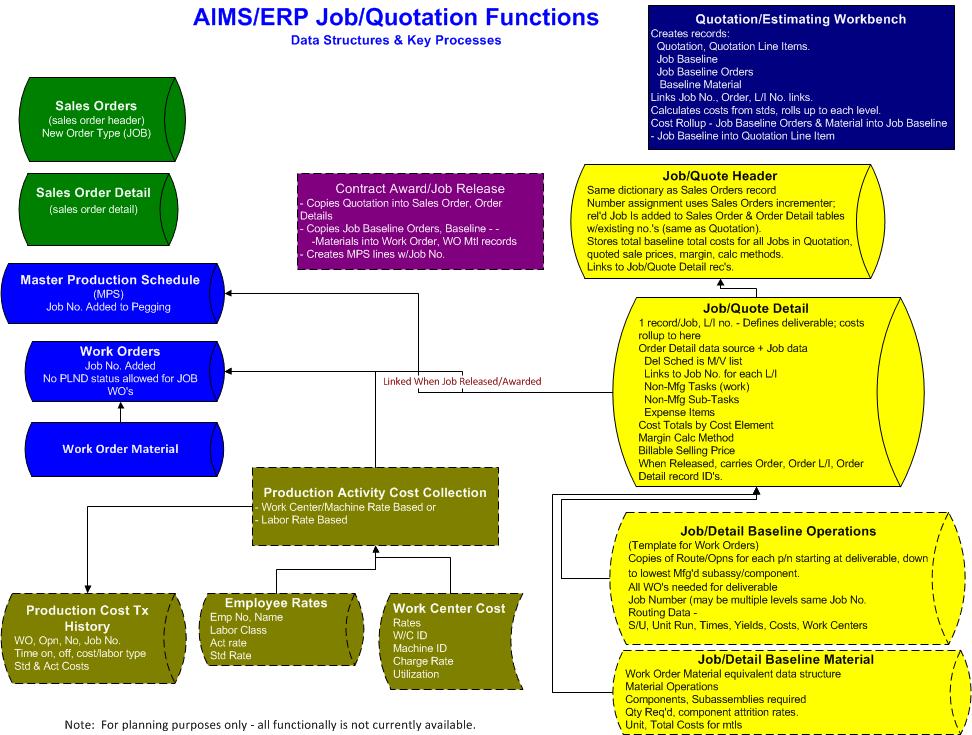
Return / Repair system - AIMS/ERP includes a very
detailed Return & Repair subsystem, all fully integrated with all other
AIMS/ERP functions, such as inventory and sales orders. While it
provides the serial-number robustness needed for more complex products,
it can and was used for more typical "RMA" functions where the returned
units/product quantity is received, examined, and dispositioned as a
result of the examination/inspection. The diagram below
provides an overview of this uniquely powerful function:
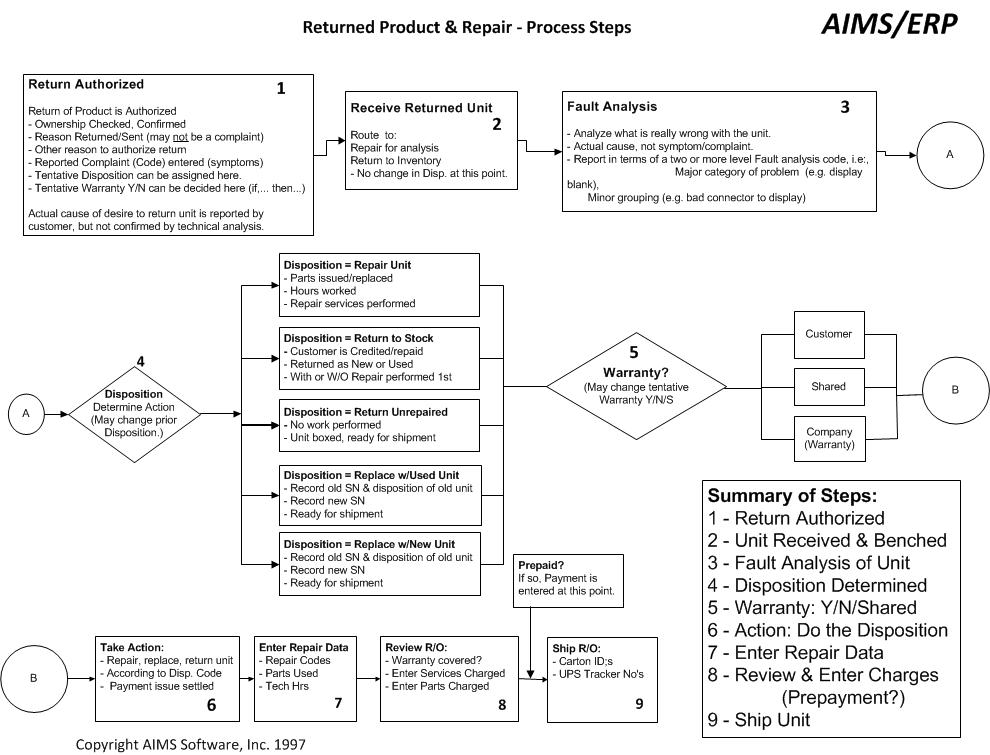
AIMS/ERP Prospects, Vendors & Customer Data Tables &
Structure - In order to provide the complex set of functions
needed by the diverse AIMS/ERP customer-facing functions, the foundation
is its sophisticated contact data tables and the way they are linked.
Unique to this design is the ability to quickly & easily add new types,
with a new table with type-specific data fields, which are automatically
linked to the primary contract record - all without code changes.
This structure is illustrated in the diagram below.
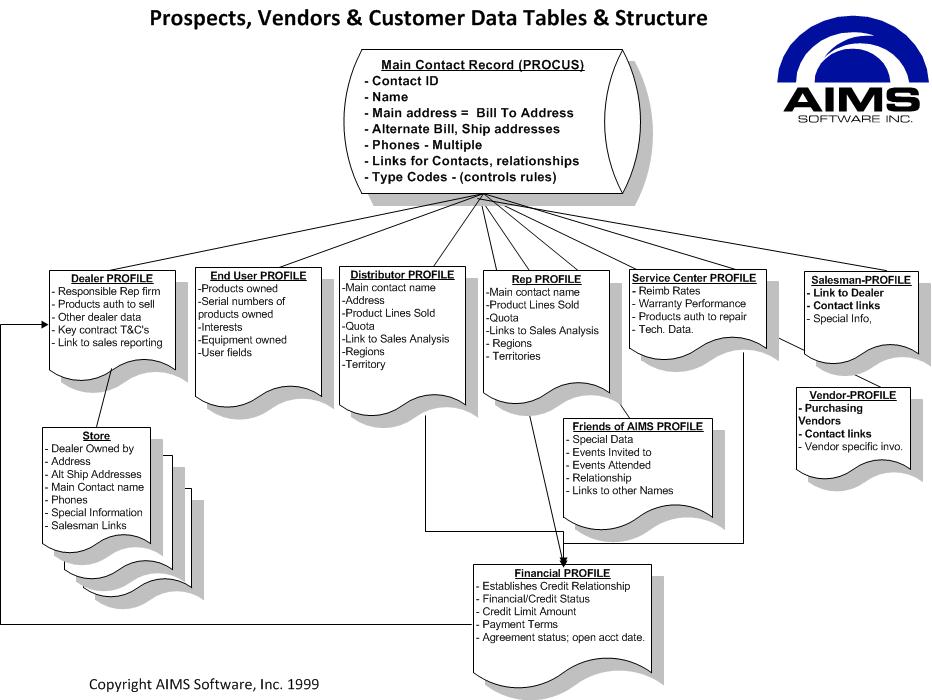
Shipping - AIMS/ERP includes a complete
pick/pack/ship process that can concurrently include both regular picked
& staging activities, integrated with a assemble-to-order functions, and
includes Shipping documents, capture of shipper tracking number data and
related activities.
Credit & Receivables Management - the CIM functions
include a complete credit and accounts receivable module that is tightly
integrated to all related functions. It handles all forms of
payment, pre-payments, credit memo, application of payments to invoices,
aging reports, credit limit control, transaction registers, and a family
of reports. Invoices are closely linked to sales orders, including
unshipped (and thus un-billable) quantities. The Return/Repair
Order subsystem is also tightly integrated with the credit & receivables
functions. There is als Pro Forma invoice support for
international shipments & related purposes. Financial reports,
such as Cost of Sales are provided to simplify month-end journal entries
into an external GL system.
Design Documents - These documents are avaialble
that you can view/download. They describe all of the tightly
integrated, customer facing functions within AIMS/ERP.
Customer Interface Module - Data Tables specification -
PDF at THIS Link
Customer Order Shipping Specifications -
PDF at THIS Link
Customer Sales Maintenance Specifications -
PDF at THIS Link
Customer Sales Orders Specifications -
PDF at THIS Link
Customer Sales Procedures -
PDF at THIS Link
Customer Credit & Receivables Management Subsystem Specifications -
PDF at THIS Link.
|