Purchasing - Procurement Management
A core feature of AIMS/ERP's "Beyond MRP" functionality is the
Scheduler which synchronizes purchased material & services tightly to a
valid schedule. "Valid" means that dates are not in the past, are
calculated from the latest work in process status, and are in correct,
logical relationship to all other activities. See the Scheduler
page for additional detail on how dates are scheduled.
For purchased material, since material is attached to specific steps
in the routing - on or off-site - AIM/ERP produces several distinct and
separated demand/supply review processes, described in more detail in
the Purchasing section of this site. All purchased material
includes what is needed, the quantity required, the date needed, and
WHERE it is requiried.
- Inbound Purchased Material Demand & Supply - these are
items to be delivered for on-site production steps.
- Drop-ship Demand & Supply - these are items to be purchased but
shipped directly to off-site contract vendors for completion of
production steps they perform.
Prioritized Buyer Actions - in each of these data
streams/displays each part number's demand/supply status is analyzed and
assigned an Exception Code, depending on how urgent buyer action is, or
is not. This unique function (not part of any "standard" MRP
system we have ever worked with, including SAP and Oracle), is developed
as follows:
- Calculate when the projected inventory for the Part
Number becomes negative - when demand is greater than projected
supply.
- Compares the projected negative inventory date with the system
parameter expedite window, the time required for placing a PO, and
the calculated lead time for the part number.
- Assign an Exception Code of 1 to 7 based on when projected
inventory turns negative, with 1 being demand within the Expedite
Window, but no PO at all.
- If projected inventory never turns negative, consider
demand & supply data to assign a code from 7 to 10, with 10 being
inventory on hand, but no demand, and no PO supply.
- Apply the Late Days Filter in the calculation process to
reduce/minimize "nervousness" in this process.
Since the Exception Codes are part-number specific, they are used
within the Buyer Work Bench to prioritize buyer actions, and within
inventory valuation reports to develop metrics for how well the demand /
supply balancing process is working - how well the buyers are keeping
inventory controlled, late (or early) PO's and others.
This unique design provides - as one would expect - substantial buyer
productivity improvements over "standard" MRP systems.
We have retrofitted this logic into other traditional MRP systems
with some success in improving buyer productivity, since traditional MRP
system do not prioritize the work for the buyer according to the
time-urgency of the action needed.
These data streams drive Buyer Workbenchs
that provide a very efficient, highly automated way of originating
purchase orders, and another for reviewing and generating PO Changes
that result from Scheduler updates.
Purchased Services - one of the shortcomings of many
MRP systems is that purchased services must be charged to an indirect
cost GL Account. This is because is is not "Direct Labor" cost.
In AIMS/ERP, purchased Services is a Direct Cost, with functioning
similer to Direct Labor and Purchased Material. So the handling of
Purchase Orders for outside/contract manufacturing in AIMS/ERP is fully
integrated into all other functions.
Trading Companies / intermediaries - Another key PO
function is the ability to acquire services or material through
intermediary companies. This enables the procurement function to
work with smaller - lower cost - vendors in foreign countries that are
represented for export purposes by a trading company. So AIMS/ERP
Purchase Orders have four distinct parties to every PO:
- Buy From - makes the material or provides the service.
- Pay To - who will send the invoice & will be paid.
- Deliver To - where the material is to be shipped/delivered.
- Bill To - who the Pay To Vendor is to send the invoice to
(normally, the company).
This very flexible, yet easy to use structure allows for efficiently
handling even complex procurement arrangements, yet in a way that is
easy to automate. This same structure allows for projects where
sub-contractors are involved.
Buyer WorkBench - These powerful tools are
essentially an initial process that organizes and sequences - in a work
Queue - all related data needed for very fast Buyer review & action.
The Work Bench window itself functions as a presentation window where
the Buyer actions are finalized. There are also provisions for
completely automatic PO generation, further speeding the process.
The work bench is integrated with the quotation function, making
completion of new PO's, often an administrative bottleneck, fast and
efficient. Our experience managing and working with procurement
functions earlier in my career taught us that buyer productivity is a
major problem in most companies. When we designed the AIMS/ERP
functions, speeding this process up while retaining as tight a control
is needed - in the buyer's viewpoint - was a major design objective.
So the combination of a prioritized work queue and queued related
information for each purchasing action results in a very fast, yet
accurate and controlled buyer action environment.
The diagram blow summarizes how the Buyer Workbenches are generated
from scheduling & other data. "REQBENCH" is the program that drives the
actual Buyer Workbench window and the queues so it runs very fast.:
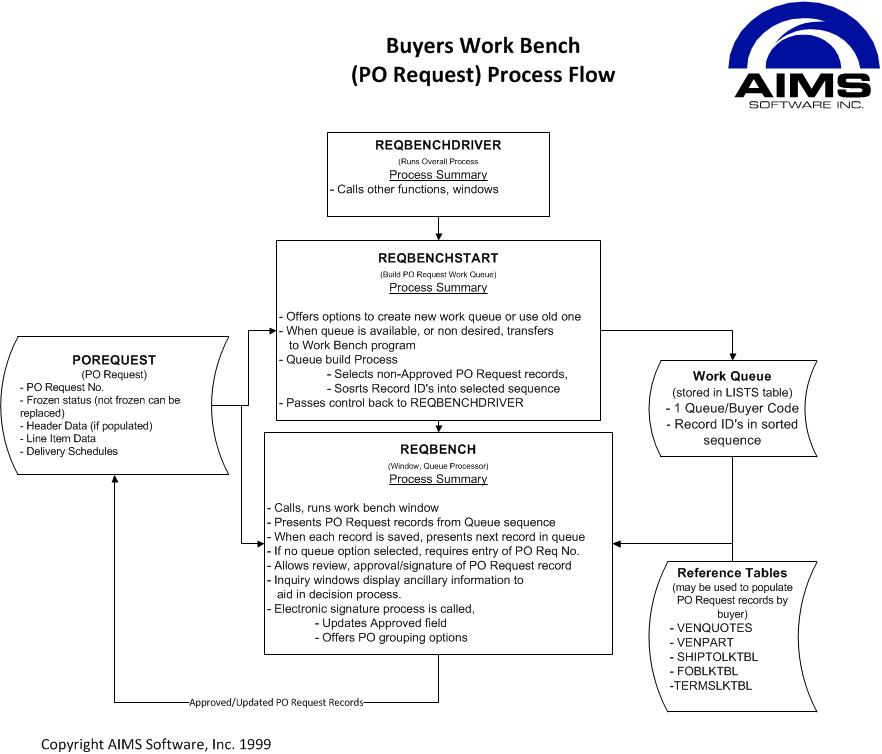
Document links:
Purchase Management Specifications - this document articulates the
design and general use guide for all purchasing-related functions in the
AIMS/ERP system - at
THIS link.
Purchasing Tools Training - this document provides detailed training
on how to use the advanced procurement tools in AIMS/ERP - at
THIS link.
|