Inventory & Material Management
The Inventory section includes the AIMS/ERP Quality Management
functions.
AIMS/ERP includes 32 different inventory movement transactions that
cover every movement scenario normally encountered in an inventory
management environment. Since AIMS/ERP was built from scratch to
accommodate off-site material movement, there are transactions for these
activities as well.
Also built into the system is a complete Cycle Counting & Physical
Inventory subsystem, that also provides for physical count and
confirmation processes for inventory at vendor locations. This
module prints tags, including for off-site inventory counts. In
the first use of this module at Alesis corporation, a team of auditors
were sent to Taiwan, where the company had a number of production
partners, to count and reconcile inventory at these locations.
This work - fortunately - went as expected.
Key features of the AIMS/ERP inventory functions include:
-
Quality control integration - movements/transactions to reflect
the various states of discrepant material, to/from any location or
inventory status.
-
Return/Repair Order integration - transactions for spare parts
used to repair returned products.
-
Sale Order Shipping - integration with picking/staging/shipping
functions.
-
Mixed Mode Production - concurrent support for traditional work
order pick list transactions, with repetitive production
backflushing ("post deduct").
-
Part Number changes - support for redesignating any quantity of
material from one part number to another. This function is
also integrated into Multiple Products Work Orders so a product can
start production in a generic mode under one part number, with
completion transactions identifying the final Part Number / product
configuration - all without losing visibility or production
scheduling control. This function is unique to AIMS/ERP in our
knowledge.
-
Warehouse to Warehouse transfer orders - includes pick/ship list
to prepare a shipment, then item by item receiving.
-
Detailed history - every inventory movement is recorded in all
detail in the inventory transaction history table, including before
and after on hand balance effect, creating in effect, a running
balance register. This function can, as a result, also provide
system integrity validation and audit as any discontinuous change in
on-hand balance is immediately apparent.
Quality Management - the AIMS/ERP quality management
subsystem provides an extensive, tightly integrated set of functions, to
identify, track, control, disposition and report on all forms of
discrepant material. The diagram below provides an overview of the
AIMS/ERP DMR subsystem:
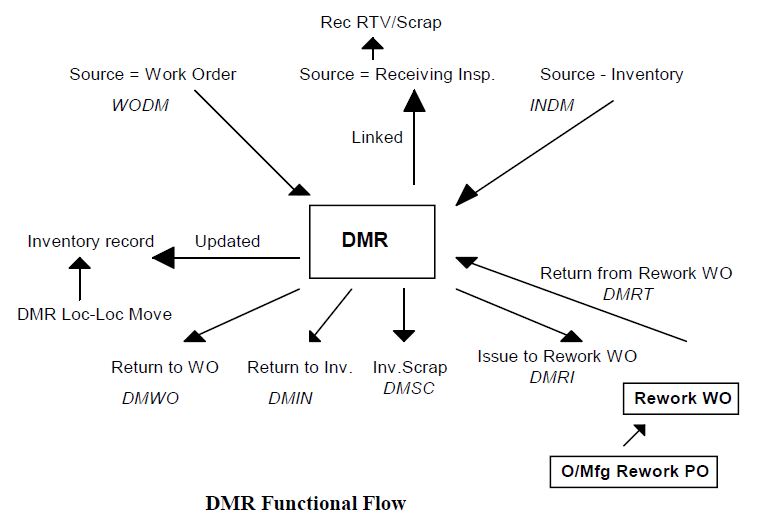
The AIMS/ERP DMR subsytem includes detailed functions in these areas:
-
Receiving Inspection Rejections
- incoming purchased material inspection rejections - transfers to
DMR subsystem.
-
Work Order - Production Rejections
- either produced items or components that are identified on a work
order as being discrepant - transfers to DMR subsystem. This
includes items - either produced items or components - found
discrepant at a vendor's facility.
-
Inventory (warehouse stock) -
can be transferred to DMB subsystem from regular stock.
-
Rework cycle management -
includes all dispositions, use as-is, repaired, scrapped, return to
DMR/MRB for reinspection, etc.
-
Material Review Board (MRB) -
full process tracking and identification with quantity
reconciliation - to make sure all discrepant quantities are
accounted for via one disposition transaction or another.
-
Detailed Disposition Transactions
- AIMS/ERP provides discrepant material disposition transactions for
every possible situation, beyond the accounting-only capabilities of
many ERP systems. These transactions are designed to mirror
the physical actions taken to dispositions so the on-hand balances
in every material status reflects reality.
-
Tag generation & printing -
discrepant identification requires positive identification; AIMS/ERP
DMR process includes the printing - at any system-accessible
location - of tags with a unique DMR number, so it can be positively
tracked & controlled.
-
Discrepant Material Reporting -
AIMS/ERP includes a family of reports to age, track and provide
historical reporting & metrics on rejected material from all sources
and all dispositions.
Documents - These documents define all AIMS/ERP
inventory functions, except reports, with the procedures providing
training and on-going reference for how warehouse staff are to perform
each transaction, and under what circumstances.
Inventory Management Specifications - design and
overall use guide at
THIS Link.
Inventory Management Procedures - detailed inventory
procedures for each situation & its associated transaction; step by step
guide for actions performed, before, during and after actual transaction
entry in AIMS/ERP; at
THIS Link.
Quality Management Specifications - design and overall functional use
guide for the AIMS/ERP Quality Management functions, at
THIS Link.
|