AIMS Software, Inc. - Home / Overview
The enterprise software development project that became known as
AIMS/ERP began at Alesis Corporation in early 1993. I had worked
on several very successful projects with Alesis during 1992 (see the
"Consumer Electronics Success Story" on the
Success Stories page).
By spring 1995, all of the modules/functions that Alesis needed has
been completed and were in stable, live use. The following winter
we launched AIMS Software, Inc., to bring the product to market. By the
time AIMS Software was closed in 2001, we had written over 1,600 pages
of detailed specifications, and the system had grown to over 1,000
screens, over 6,000 data fields, and over 400 tables, and had been
purchased by 10 companies. Almost all of this documentation is
available on this site. You may download it and use its ideas
if/as you find useful. You can also view a detailed sales brochure
at
THIS Link.
Alesis had purchased 3 different packaged ERP system, 2 of them very
well known, established systems, yet all had failed due to serious fit
problems. So AIMS/ERP had to go well beyond what the "standard"
systems did to work, and this it did. Fortunately, we were
informed by major ERP system experience from prior work, and knew what
the opportunities were.
Besides the kind of essential functionality normal to all ERP systems
- inventory control, purchase orders, bills of material, cost rollups,
material planning, etc., AIMS/ERP has a number of unusual, advanced
design features, not found as integral functions in even "world-class"
ERP system. Or, if these capabilities are provided, their use is
complex and tricky.
These key AIMS/ERP unusual features include:
-
High Performance data structures -
key AIMS/ERP tables used data structures which eliminate
almost all I/O, making the system extremely fast. In a
technical feasibility demonstration paid for by a division of
Raytheon, Cedarapids, the system scheduled ("exploded") a 14 level
product structure with over 250,000 parts for a huge road paving
machine in 2 1/2 minutes on a 75 Mhz PC, far faster than their IBM
mainframe. They bought the system...!
-
Bill of Manufacture data structure
- in which the routing (how a product is made and/or work performed)
is the primary data, with purchased material linked to specific
steps, which can be off-site, or in-house, in the routing.
-
Named routes - instead of the
"standard" part number specific routings for production, AIMS/ERP
require only that the company setup one routing for each
production/work/material flow. This dramatically reduces the
data management required.
-
Advanced Scheduler - this
function schedules all work, using the routing data, and from these
dates, determines when - and where (in-house, or at a vendor) which
material is needed. We called this "beyond MRP" functionality
(white paper
here). The Scheduler logic includes:
-
Indpendent demand control -
managed in the Master Production Schedule data; sets the
"complete by" target dates.
-
Dynamic Work Order schedules
- all work orders are scheduled the same way, whether "planned"
or in progress.
-
Back scheduling - from
independent demand, and down through the product structure.
-
Compressed scheduling - when
insufficient time to complete tasks, a compression process is
used to "squeeze the dates".
-
Forward scheduling - if
compression failes, the scheduler pushes all date forward,
including UP the product structure.
-
Projected Days late - since
the Scheduler can push completion dates out past the original
MPS dates, the system keeps track of the original completion
date and the currently projected completion date, providing the
data for a "Projected Days Late" report that highlights likely
problems BEFORE they occur.
-
Drop/Direct Ship Demand & Supply
management - since AIMS/ERP can schedule material to be
delivered from a purchased material vendor directly to a contract
production partner, a whole separate demand/supply ("MRP" process is
provided; we have not seen anything like this in ANY ERP system to
this date.
-
Multi-channel sales - AIMS/.ERP
provides detailed support for multiple types of customers - each
with its own product catalog, pricing, and related data; essential
for maintaining "who can sell what" agreements with licensed
distributors globally.
-
Sales Order Configure to Order -
sales order based configurator; linked to a fast, easy to use
assembly process seamlessly integrated with sales order
pick/pack/ship process. (most other configurators use linked
Work Orders; more complex).
-
Component level optimized sales
forecasting - sales history for configured production is
captured at the component level, not the parent item.
Forecasting uses a multiple algorithm, best-fit selection process
that is a proven best practice for all items, including components
of ATO products.
-
Concurrent multiple mode operation
- AIMS/ERP provides the ability to concurrently manage job/project
work using estimates and quotations, intermittent batch production,
and repetitive manufacturing, all using the same tools and
functions.
-
Integrated on and off-site production
- since AIMS/ERP schedules work to be performed, regardless of what
or where it is, any production/work/material flow can be any mixture
of off-site, on-site, in and back out, work flows, including ocean
shipping, other transportation, customs clearance, trading partners.
All of these steps can be linked in a seamless flow, a sequence of
steps that is scheduled and tracked in a standardized,
straightforward way.
-
Dimensionable material support - AIMS/ERP can accept a list of pieces
to be cut from standard material, without having to assign part numbers
to each piece, then calculate how the pieces should be cut, displaying a
visual image of the raw material, such as a sheet of metal or plywood.
While drawing pictures of parts is certainly not new, to our knowledge,
the ability to identify specific parts, yet not bury the system with
part numbers that may only be used once, and have an existence only in
work in process, is unique.
-
Multiple products production -
AIMS/ERP has the ability to schedule production of one "generic"
part number, then complete that production by assigning a different,
variant part number. This function provides a major
simplification in scheduling and producing famlies of similar
products, since the variants to the generic item do not have an
identity until they move to finished goods inventory. The mix
of variants can be varied as needed, as close-in demand fluctuations
appear, all under a single production work order and schedule.
Functional Overview - the diagram below is a
high-level illustration of the integrated functionality that ewe
designed into AIMS/ERP.
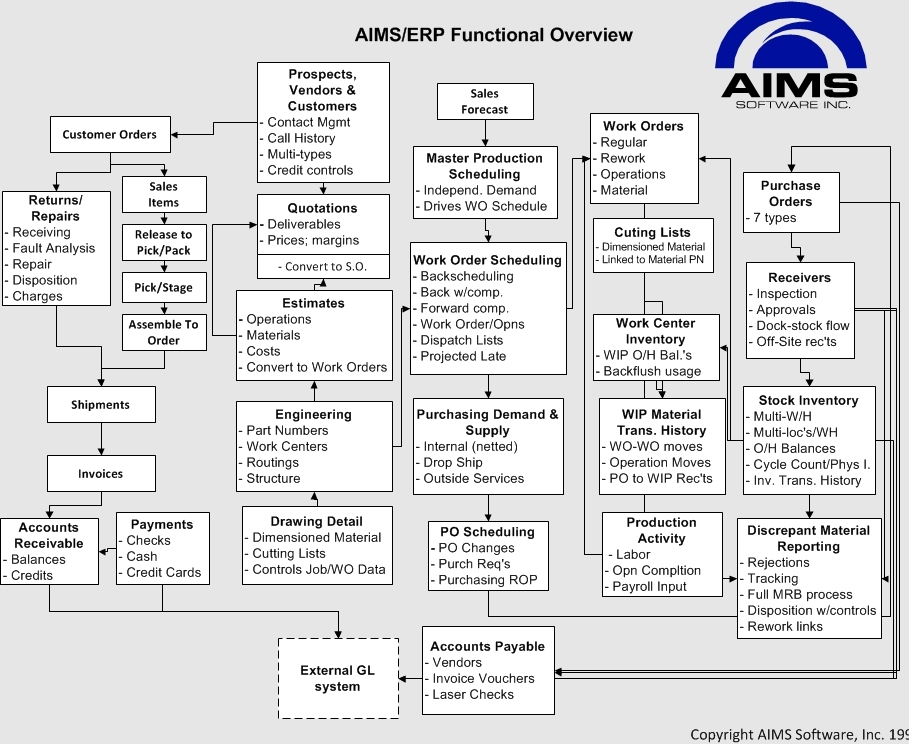
We decided to build this sub-site so other
could, at their own pace and direction, learn about one of the most
remarkable projects that we were honored to do in our career.
AIMS/ERP was fun to design, more fun to see developed and in use, as it
solved a long list of problems that were then, and still are, normal to
ERP system, their implementation and use.
Best was seeing how its truly functional
software and amazing speed helped companies perform better, first
Alesis, which nearly doubled in size - from $40 to nearly $90 mil/year
in less than a calendar year, and then other AIMS Software customers.
We closed the company in 2001 after Y2K essentially destroyed demand for
ERP system. We concluded that it would never make serious money,
and so shut it down, still in the black.
Documents - AIMS/ERP Functional Overview - this
is one of the sales brochures we used during the active years of AIMS
Software, inc. and shows in fair detail all of the functions that
AIMS/ERP included, and some detail about how they work. It
includes a number of graphics that speed understanding. It is
available at
THIS Link.
Complete list of AIMS/ERP Design
Specifications - this single document lists all of the primary
design specifications that were written to drive the design, validate
testing, and provide user documentation. It is available at
THIS Link.
|