Engineering - Product & Project Engineering
This module is designed so that literally anything can be scheduled
and linked to form a network of work tasks that the Scheduler generates
start and complete dates for each activity. These activities can
be internally performed at a production work center, externally
performed by/at a vendor partner, or support scheduling of activities
such as ocean shipment.
Material is linked to specific tasks where it is called for, which
can be either internal or exterenal.
This unique data structure is illustrated and
summarized below:
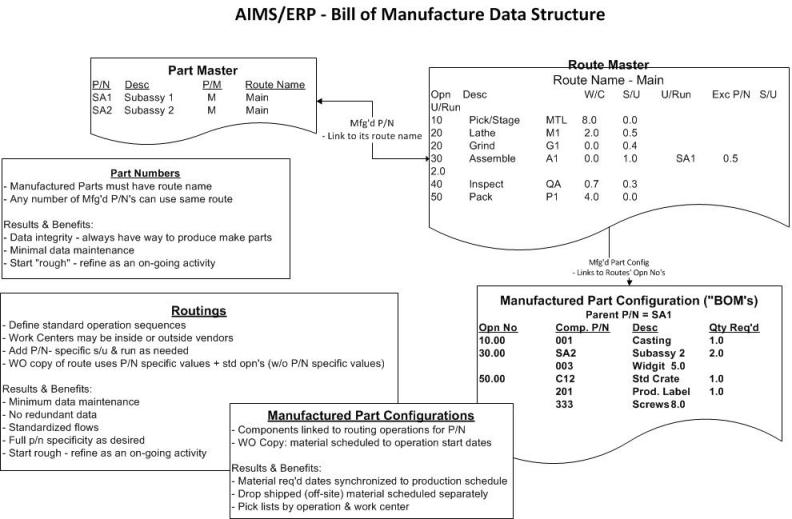
Key advanced design features of the Engineering module
include:
Named Routes - the routing data exists independently
of any Part Number. We learned early in our career that the
routing data in ERP systems where the routing is linked to each part
number is invariably the most out of date and least accurate data.
Since traditional MRP systems do not use this data for scheduling
anything, the set up & run time data becomes mostly a cost accounting
interest.
AIMS/ERP has a full-scale scheduling system, and so depends on the
accuracy of the routing data to generate an accurate schedule.
We also learned early on that in most production situations there are
a fairly small number of material flows - or if not, there should be as
a best practice. This renders much of the normal routing
data redundant and repetitive, so the copy function is needed for data
management, except that updating all of the copies becomes impractical.
Exception oriented routing data structure - since
routing data is copied into Work Order data stucture, where scheduling
is performed, AIMS/ERP allows for a standardized routing flow to be
defined, with Part Number specific exceptions to be identified at any
step in the flow. When the routing data is copied into a Work
Order, these exceptions are copied, resulting in a Part Number-specific
route, but consisting mostly of standardized data.
Operation Linked Material - purchased material is
linked to a specific operation in the route, which may be an internal or
external (vendor) work center. This key design feature enables
AIMS/ERP to vendor specific requirements for purchased material, and
ultimately is the basis for the Drop Ship Demand & Supply functionality
in the Purchased/MRP functions.
The Engineering Management Design Specifications & guide to
use may be viewed and/or
downloaded via the PDF at
THIS link
|