Scheduling - Production & Activities
This is the most powerful module in the AIMS/ERP system. It
uses the Bill of Manufacture data structure coupled with Work Order data
structures that are fully populated, and that can be individually modified
or created from scratch even
while in a "planned' status, with only the dates being changed.
This method supports project-oriented, engineer to order, build-to
order, assemble-to-order (from configured-to-order sales
orders),one-off, repetitive and periodic production all concurrently.
Routing steps can be internal or vendor-performed, allowing a complex
mix of work and material flows.
Scheduling in AIMS/ERP is driven completely from the Master
Production Schedule function - which defines and controls all
independent demand. The process backschedules from these dates,
uses a compression algorithm to attempt to fit potentially late work
steps into the schedule (there are no "past due" dates in AIMS/ERP), and
if this fails, will forward schedule UP the product structure, pushing
out the projected completion dates, all while retaining the originally
scheduled dates so they can be compared.
Projected Days Late - this function / report
identifies scheduled production that, if not changed, will result in a
later completion date than originally scheduled in the MPS. No MRP
systen can produce this kind of data.
For purchased material, since material is attached to specific steps
in the routing - on or off-site - AIM/ERP produces several distince and
separated demand/supply review processes, described in more detail in
the Purchasing section of this site. All purchased material
includes what is needed, the quantity required, the date needed, and
WHERE it is requiried. These data streams drive Buyer Workbenchs
that provide a very efficient, highly automated way of originating
purchase orders, and another for reviewing and generating PO Changes
that result from Scheduler updates.
- Inbound Purchased Material Demand & Supply - these are
items to be delivered for on-site production steps.
- Drop-ship Demand & Supply - these are items to be purchased but
shipped directly to off-site contract vendors for completion of
production steps they perform.
Prioritized Buyer Actions - in each of these data
streams/displays each part number's demand/supply status is analyzed and
assigned an Exception Code, depending on how urgent buyer action is, or
is not. In the WorkBench the buyer's default (other options are
available) work sequence is to work on the most urgent part numbers
first.
Manufactured Part Demand & Supply - there is a
separate demand/supply stream display but it needs little or no review
because of the fact that ALL work orders - planned and in process - are
scheduled in the same way, keeping demand & supply under control.
A White Paper, "Synchronized Production & Material - Beyond
MRP" - explains how the advanced synchronized scheduling of
production & material is different from the 40 year old MRP model and
its inherent disadvantages. The PDF of this paper can be
downloaded at
THIS link.
Below are two diagrams that illustrate how the AIMS/ERP synchronized
production & material process works, including an example of a complex
inside/outside production & material flow works. Some
of the extensive documentation for how the scheduling process functions
can be downloaded at document links below.
AIMS/ERP Production & Material Scheduling Steps -
are summarized in the diagram below:
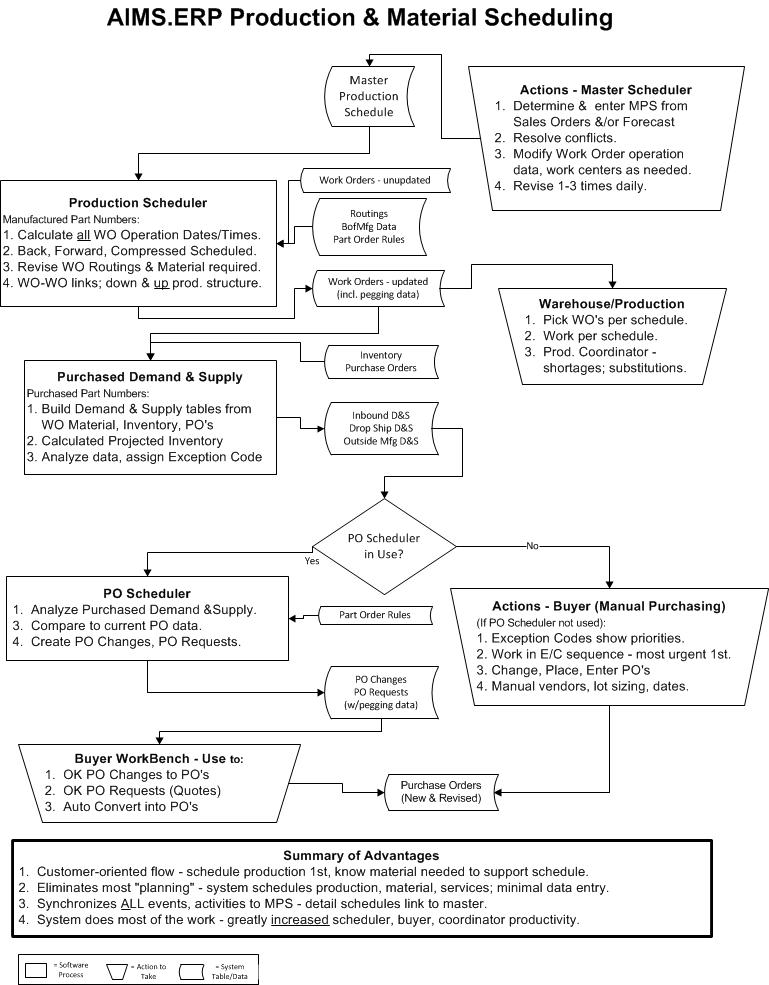
Outside/Contract Manufacturing - AIMS/ERP was built
specifically to support a complex off-site flow of material through any
number of combinations of procurement, direct shipment, vendor-to-vendor
shipments of intermediate products or subassemblies. The diagram
below summarizes how this flow functions.
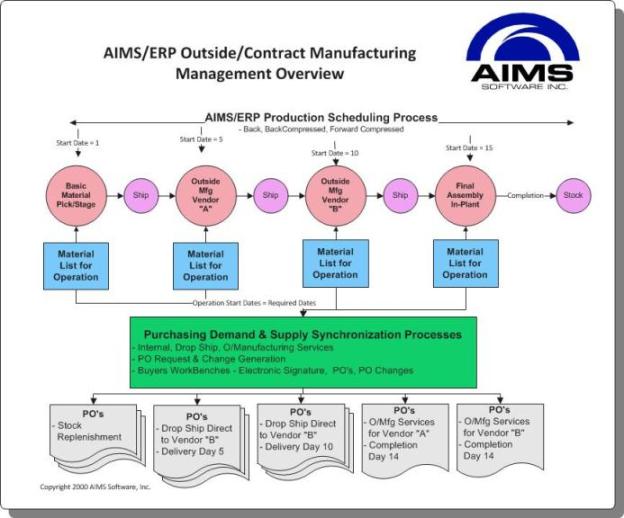
-
AIMS/ERP Scheduler - Documents -
Scheduler Specifications - this is the detailed
software design specification for the core scheduling process -
PDF at THIS Link.
Training - Using the Scheduler Guide - -
PDF at THIS link.
|